Sunday, October 30, 2016
Thrill Seeker to the winter storage again
Saturday, October 29, 2016
put a final layer of glass over the outside of the cradle
In the morning we did some prep work as sanding and routing some edges of the wood to laminated the outside with the last layer of glass. The vertical panels will be tape to this glass work after they are glassed to. I put some putty in the sharp corners before we put the glass over it. The vacuum is very help full to get everything nice flat and in the corners.
Friday, October 28, 2016
some more stuff for the cradle
Thursday, October 27, 2016
Gluing the center support of cradle on it
I took today free to work on the cradle again, it all takes longer than expected and it is a lot of work.
We used the old battens of the mold frames so this clears the pile of wood we still have. Fetske cleared the battens of packing tape while I cut the support frames. These had to be shorter because the side battens of the cradle where now in place. the next job was to fill the gaps between the supports what I made of two layers triplex. I filled the space in between also with two layers of triplex. After that all was in place I could start with gluing the battens on it. But before we could do that we first sanded the the rest of the packing tape of it what was still left on some places.
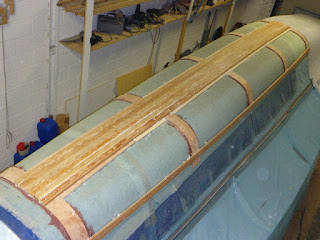
We used the old battens of the mold frames so this clears the pile of wood we still have. Fetske cleared the battens of packing tape while I cut the support frames. These had to be shorter because the side battens of the cradle where now in place. the next job was to fill the gaps between the supports what I made of two layers triplex. I filled the space in between also with two layers of triplex. After that all was in place I could start with gluing the battens on it. But before we could do that we first sanded the the rest of the packing tape of it what was still left on some places.
Tuesday, October 25, 2016
placing triplex strips on the cradle
Sunday, October 23, 2016
Unpacking the cradle
I had some computer troubles on my work yesterday evening and today so I could not do much, but when I arrived at home I did see that Fetske was still on some working clothes and told me she had unpacked the cradle. This are things I like it ;-). The peel ply is still on it because the laminate has to harden more. We did use 50% slow harder en 50% standard harder because we were afraid that we were not quick enough to do it only with standard harder. We found out that after all it maybe was possible .
Saturday, October 22, 2016
Laminating the cradle
Yesterday was a bussy day, in the morning I prepared the dagger board. In the afternoon we laminated the dagger board for the last time, this time on both sides. We the went to buy some extra harder for todays job. When that was done we went to our rigger to talk about our carbon mast and to seal the deal.
Today I started with sanding the dagger board and in the afternoon we laminated the cradle for our trailer
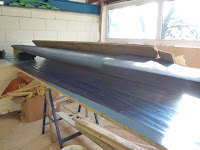
Today I started with sanding the dagger board and in the afternoon we laminated the cradle for our trailer
Tuesday, October 18, 2016
Laminated the dagger board on the other side
I took the afternoon free to laminated the dagger board on the other side. I first unpacked and cleaned it and then Fetske dropped by to assist me. We did sand some edges and cut away some carbon so it was ready to take another layer. Fetske cut some bleeder cloth and peel ply while I was preparing the vacuum back. The laminating was a quick job again. After punting on the vacuum we had a tea break and after that we cut some mold for the five wooden ribs what will be place under the cradle. I made the from the form frames of the main hull.
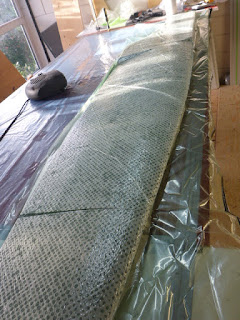
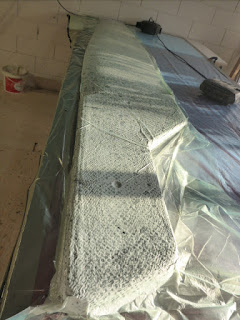
Sunday, October 16, 2016
Laminated the dagger board on one side
In the morning I prepared the dagger board to laminated one side. In this stage it weight just under 15 kg. I decided to do only one side because I can then sand the edges of the laminated so that you have a smoother surface were the layers lap over each other. An other advantage is that it is easier to do. In the afternoon Fetske did come assist me with the laminating, this was relative quickly done, so we had much time left. We did first a tea break and we than started with preparing for cradle again, I did find some old thick plastic what I put over the bleeder cloth to get some extra spacing. When that was in place we put a layer vacuum film over it to get a smooth surface. We already place the two layer of 625 gr/m2 on it. The vacuum back what is going over it all is glue on one side with tacky tape. At last we put some old vacuum film on the sides so that the stays clean when we are laminating.
Saturday, October 15, 2016
trimmed the edges of the dagger board and did a trial fit
In the morning I directly started with unpack because I was very curios about the result. After lifting out the dagger board out of the mold the result was promising. I did cut the carbon away with was coming out of the middle on the edges, after some sanding by hand the result looked very good.
I than did a trail fit in the dagger board case to see how much room I had still left for the other two layers and I have room enough so I don't have to weary about that. The dagger board has not much room to the sealing to get it in.
I then drilled the holes for the control lines, this was not easy because you have to drill to all the carbon UD layers. When I finally cut threw, I clued some tubes in place.
While that was drying I started to make a begin with cradle for the trailer like Phill did made for his F85SR. I tape the holes and I cut some glass fiber and some other pessary stuff.
Tomorrow we go further with the dagger board.
I than did a trail fit in the dagger board case to see how much room I had still left for the other two layers and I have room enough so I don't have to weary about that. The dagger board has not much room to the sealing to get it in.
I then drilled the holes for the control lines, this was not easy because you have to drill to all the carbon UD layers. When I finally cut threw, I clued some tubes in place.
While that was drying I started to make a begin with cradle for the trailer like Phill did made for his F85SR. I tape the holes and I cut some glass fiber and some other pessary stuff.
Tomorrow we go further with the dagger board.
Friday, October 14, 2016
Glued the dagger board half's together
Yesterday I put some more putty on the side's of the center piece to fill the left gaps. Today I started with preparing to glue the half's together, This time I used the other mold half to put the dagger board in. I did put some packing tape in the mold so that the half does not stick when some epoxy comes between them. I cut a piece of carbon to put between the half's to compensate the height of the center piece what is a very little to high. With one layer between them it is just right. In the afternoon Fetske did come to assist me with gluing the half's together. We first punt some putty on the foam and than laminated the carbon biax over it. We then put some putty on the other half also over the center piece and finally put some putty on the first half where the center will fit in this was well done so that there is enough to fill the gaps around the center piece. We that closed the vacuum back and put as much pressure as the pump can get (-0.95 mbar) to squeeze the half's together. After the tea break Fetske did leave and I did some sand of the last prime I did put on the hull so it is now ready to punt paint on it.
Tuesday, October 11, 2016
Glued the HD center piece in place on one site
Sunday, October 9, 2016
Laminated the centre HD piece
I started with unpacking the mold and then glued the HD pieces for the control lines of the half what was used to support the mold. While that was drying I sanded the foam away of the after edges and bottom and fill it with a HD putty. I also sanded the inside locker so it could be painted later. On the end of the morning I cut the necessary pieces for the center piece. In the afternoon we rolled the HD foam in three layer bi axial and placed it between two wooden pieces to keep it striated. After a tea break we decide to put the boat level. We use the car jack to lift one side. When it was level we put the water line with a marker on the hull, this time the lines did meet at the front at the same height. The old lines can still be seen. On the end I painted the locker.
Saturday, October 8, 2016
Laminted the dagger board mold second stage
Friday, October 7, 2016
Laminating the other dagger board mold half first stage
In the morning I put a putty mixture of glass bubbles and graphite on the dagger board half as a sort of gel coat. In the afternoon we laminated over the putty mixture with layers of glass one 400 and one 625 gr/m2. After a short tea break we painted the complete bottom with grey primer, this is the last one before the top coat and copper coat will be put on.
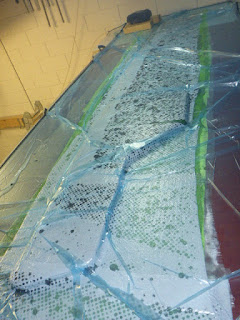
Subscribe to:
Posts (Atom)